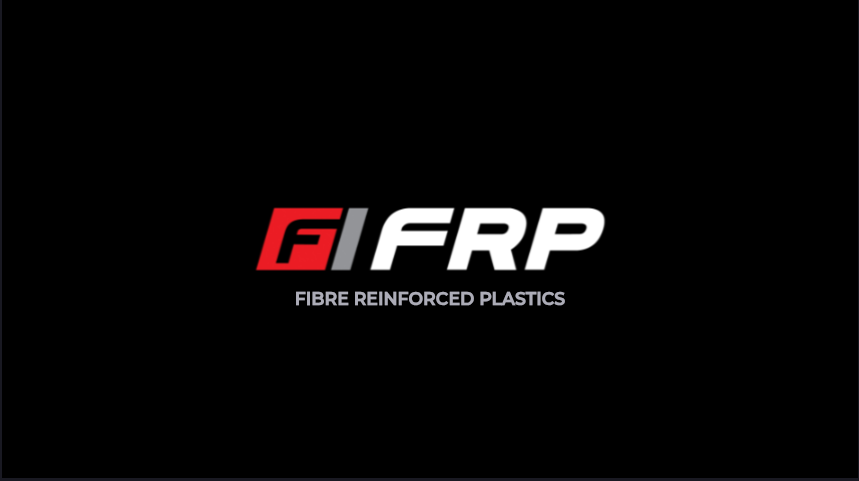
Fibre Reinforced Plastics
World-Class Fiberglass Solutions
Fibre Reinforced Plastics is a proudly 100% New Zealand-owned and operated company, recognized as a leading manufacturer of fiberglass products. We cater to a diverse range of industries, including architecture, banking, and transport, providing custom-designed solutions tailored to meet our customers’ specific needs.
At FRP, we are committed to environmental responsibility. We implement environmentally conscious practices across all aspects of our operations to minimize our impact on the planet. Our goal is to create high-quality products while ensuring sustainability and care for the environment.
Transport Applications
We specialize in manufacturing a wide range of fiberglass components and panels for campervan, caravan, and bus manufacturers. Our products are designed to meet specific requirements and include:
Body panels
Side and rear skirts
Lutons
Showers
Sinks
Lockers
Fibreglass Cladding for
Motorhomes & Caravans
Fiberglass has established itself as the most versatile, durable, and cost-effective material for cladding motorhomes and caravans. Our exterior panels can be produced in various thicknesses and specifications, with options for reinforcement in strength-critical applications.
Key features include:
A minimum 2mm fiberglass skin
Composite panels with foam cores for enhanced stiffness and insulation, featuring inner fiberglass skins
Seamless internal applications, such as shower cubicles and molded bench and countertop surfaces
Our fiberglass solutions ensure quality, durability, and efficiency for all your transport needs.
Architectural Fiberglass Features
we collaborate closely with designers and architects to bring their visual concepts to life. Our expertise extends to creating a variety of architectural elements, including hoods, soffits, fascias, cladding, and intricate interior and exterior details.
Our architectural panels can serve as non-structural cladding, or, with the use of advanced glass fabrics, they can be engineered for strength, transforming them into fully self-supporting structural components. Despite the differences in function, both types of panels maintain a consistent aesthetic appeal.
The possibilities with fiberglass are virtually limitless, allowing for complex shapes, diverse scales, and a wide range of colors and surface finishes. Architectural fiberglass panels offer building designers enhanced flexibility, enabling the creation of compound curves and custom textures tailored to specific designs.
A significant advantage of fiberglass is its high strength-to-weight ratio, making handling and installation easier. Additionally, the pre-finished nature of our products ensures cost-effectiveness compared to traditional cladding materials.
In addition to cladding, we can design and produce fiberglass columns, canopies, cornices, fascias, flashings, soffits, and more. If you need unique design elements for interiors, shop fittings, or film studios, we can create custom moldings or production runs tailored to your specifications.
Custom Design
Concept, Plugs, and Moulds
All our fiberglass products are custom-designed to meet your unique requirements. Whether you have ideas, designs, or CAD files, our dedicated R&D team is ready to collaborate with you on your manufacturing project. We are equipped with a state-of-the-art 5-axis CNC machine for plug creation and a comprehensive mould-making facility.
Plug Design and Mould Manufacture
For one-off or limited production runs, we can often create your part directly from a painted MDF mould. However, for larger production runs, we start with a "plug," which serves as the pattern for mould creation.
Creating a plug for complex parts involves preparing CAD drawings, CNC machining, and finishing the plug to precise dimensions and tolerances. Our investment in 5-axis CNC machinery allows us to produce plugs with exceptional accuracy.
Once the plug is completed, it undergoes sanding, painting, and waxing before we take a mould from it. This meticulous process ensures that every detail meets your specifications and quality standards.
Manufacturing Process
Production
Our manufacturing process incorporates a variety of techniques, including hand layup, vacuum infusion, and spray-up with a chopper gun. The choice of method typically depends on the complexity of the layup and the volume of products being produced.
Trimming and Finishing
For customers who require trimmed parts, we create custom trimming jigs to ensure precision and consistency. This tailored approach guarantees that your finished components meet your exact specifications and quality standards.
Get in Touch
Interested in partnering with a leading manufacturer of fibreglass products? Fill in your details below and we will reach out to you promptly. We look forward to connecting with you!